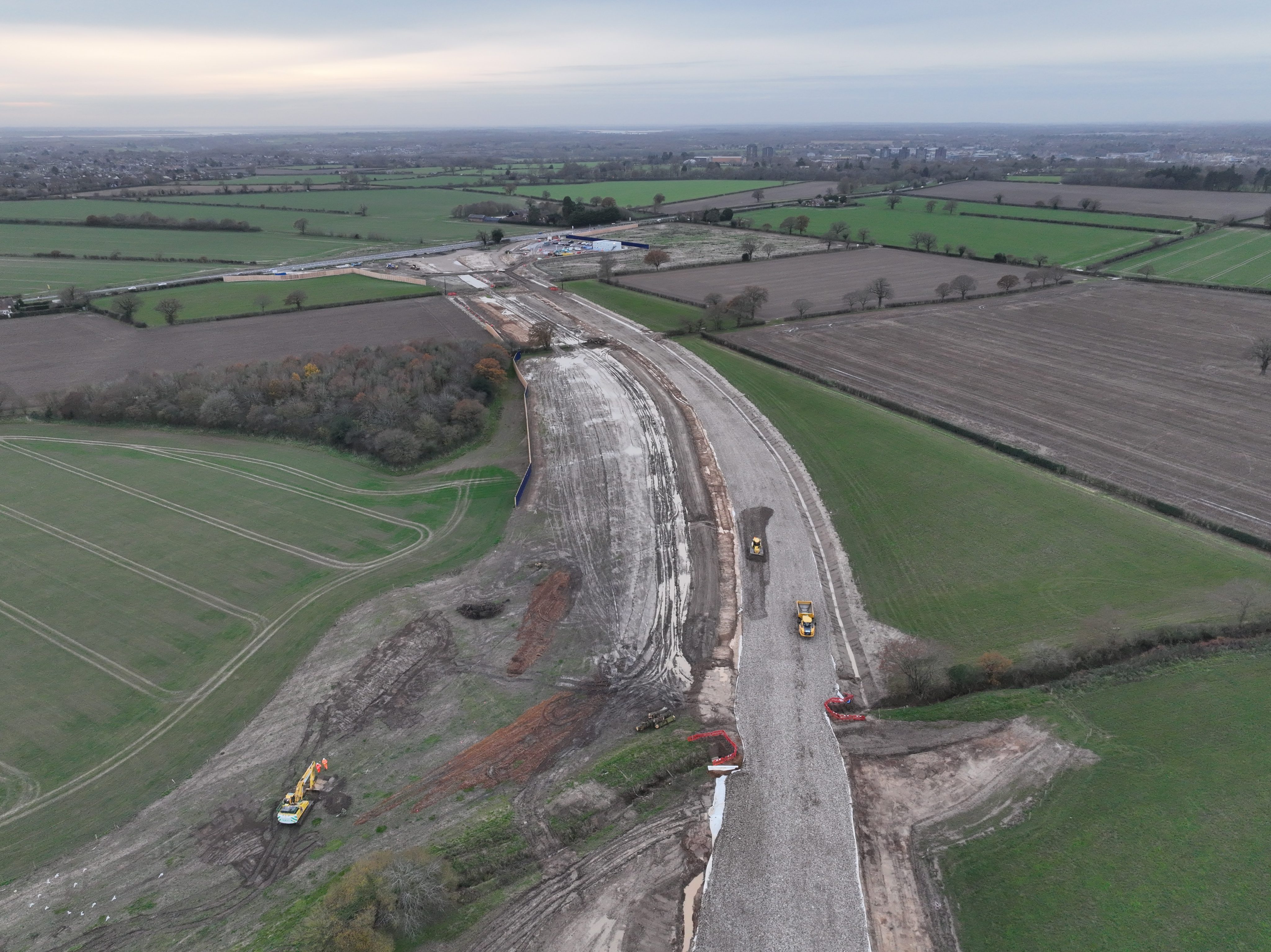
News
Spotlight – Photogrammetry surveying
A closer look at our photogrammetry UAS and how we use the data
Regular photogrammetry surveys for data modelling can give excellent insight to construction progress, maintenance scheduling, and even longer term changes over time for projects such as estuary, foreshore or headland monitoring.
If you ask aerial surveying companies when is the best time to undertake a photogrammetry, the answer will always be “as soon as possible”. The reason being that the more data you have before work starts, the better you can monitor and track changes, and plan ahead. This is the same for asset maintenance as a survey conducted now can potentially save you several times the cost of waiting for the asset to deteriorate before the damage is noticeable.
What is photogrammetry?
Simply put it is the process of taking photographs of the area or asset which is subject to the survey. However what makes the model possible is recording the location of each photograph so the modelling software can place each photograph in the correct place to build a 2D or 3D model of the subject.
With the model we can assist our clients, calculate material volumes from bulk stockpiles and cuttings, locate welfare compounds, material and equipment stores, record and plan progress, and proactively programme maintenance regimes.
How does it work?
There are two methods of photogrammetry:
- Orthographic – Using this method we position the camera at 90° to the flight plane (the altitude and flight path of the UAS) so it is directly facing the datum plane (the ground or object being surveyed). We find this method is best used for open fields or where oblique detail is not as critical to the resultant model. Most of our projects use this method as we are still able to maintain a high grade of vertical detail but as this method requires fewer passes it means we can survey a larger area in a shorter time.
- Oblique – When using this method we will angle the camera so it is at 35° from the datum plane. This allows us to capture vertical detail and is useful if there are key structures or elevations in or near to the works area, or if the survey is being taken to show progress in the middle of construction where the exact status of key features such as abutments, retaining walls, or bridges are important to the overall model.
These surveys require the UAS to pass and repass the same area from different angles to capture the required imagery, so they generally tend to take more time. However the vertical detail collected does build a more detailed model of the project.
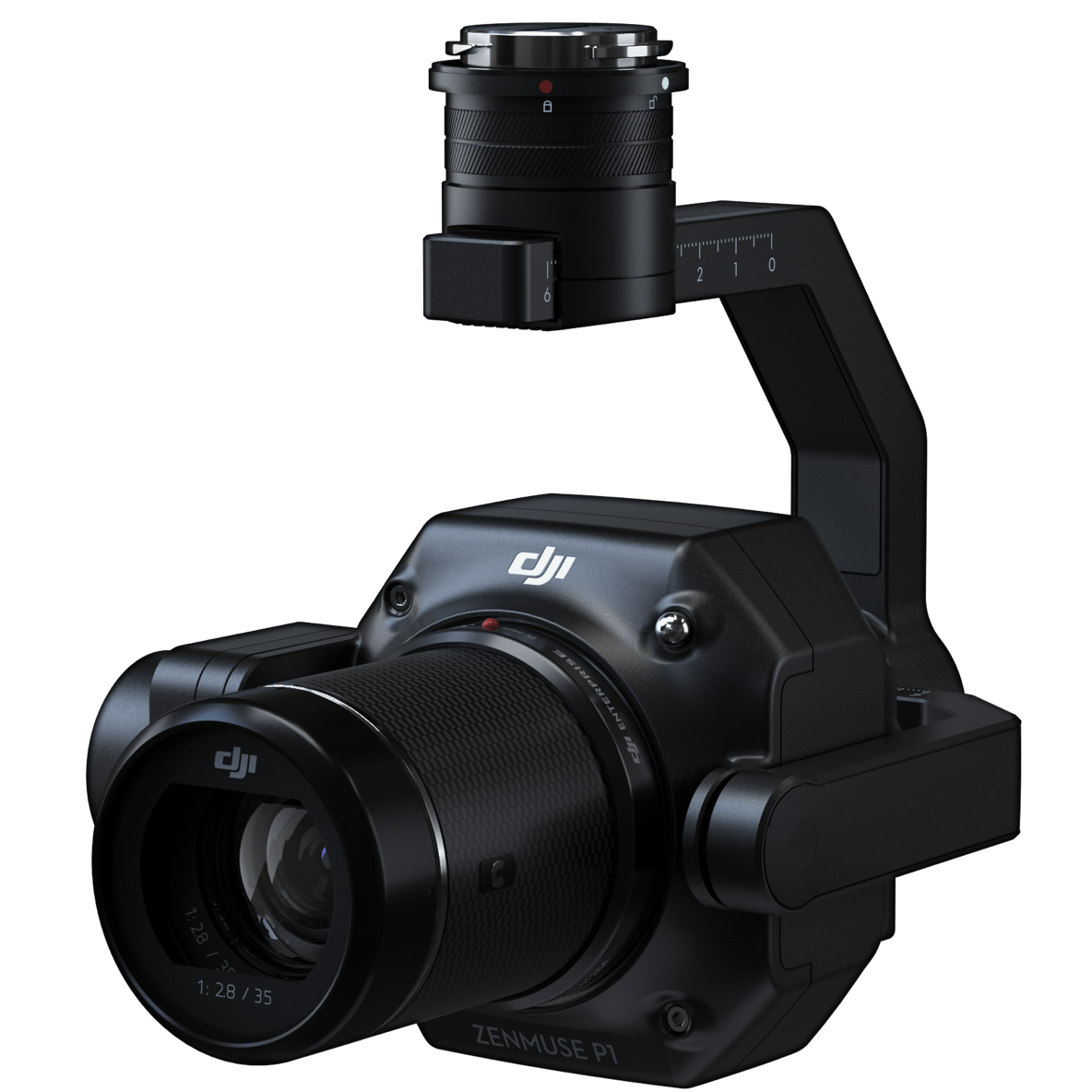
use for our orthographic surveys
– image courtesy of DJI
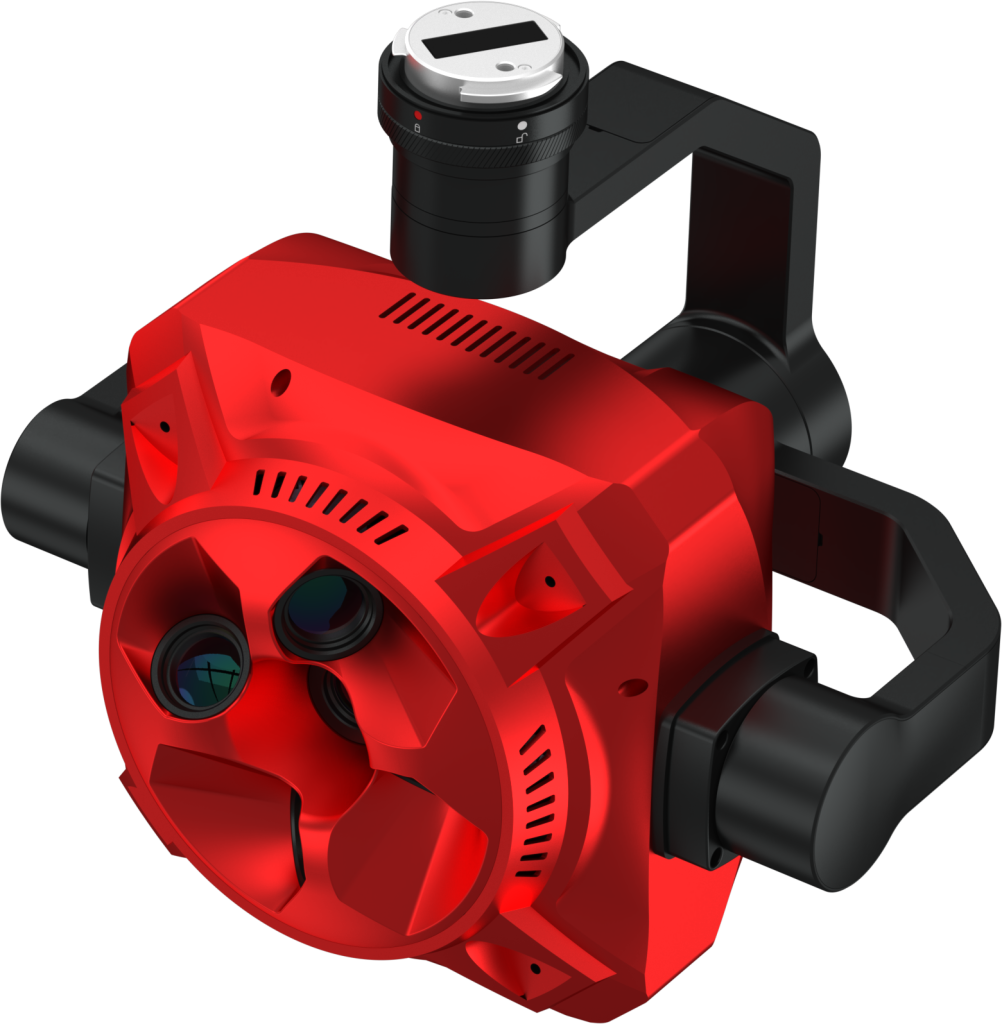
– image courtesy of SHARE
Once the UAS has flown the required flight operation we will import the photogrammetry data and the recorded ground control point data and run them through various models. We are going to go into a more in-depth study of our processing software and the choices we make in a separate study, but for now here is a brief overview of our process.
If all we require is visual detail, such as with a building condition survey, or a general progress update we will reconstruct the data model in DJI Terra as we have found its modelling engine can handle a large number of photographs and 3D modelling, even with oblique datasets, in a relatively short amount of time.
For times when we need accurate elevation data for volumetric calculations we will process the photogrammetry data through Terrain Creator and export it to Virtual Surveyor. While it is not a true 3D engine (the creators describe it as 2.5D) – vertical surfaces will render as a stretched image of the ground below rather than show any detail – the accuracy of the data and ability to interrogate the data in more ways, such as generating cut and fill measurements, or track and calculate stockpile volumes is more important than the detail in the vertical surfaces of nearby buildings.
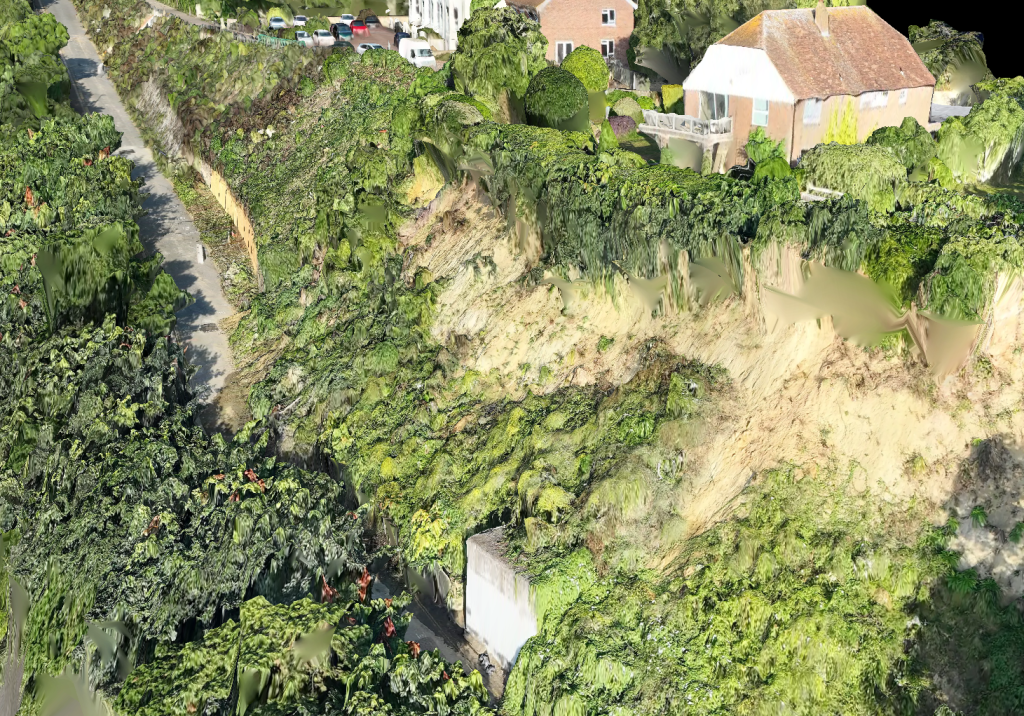
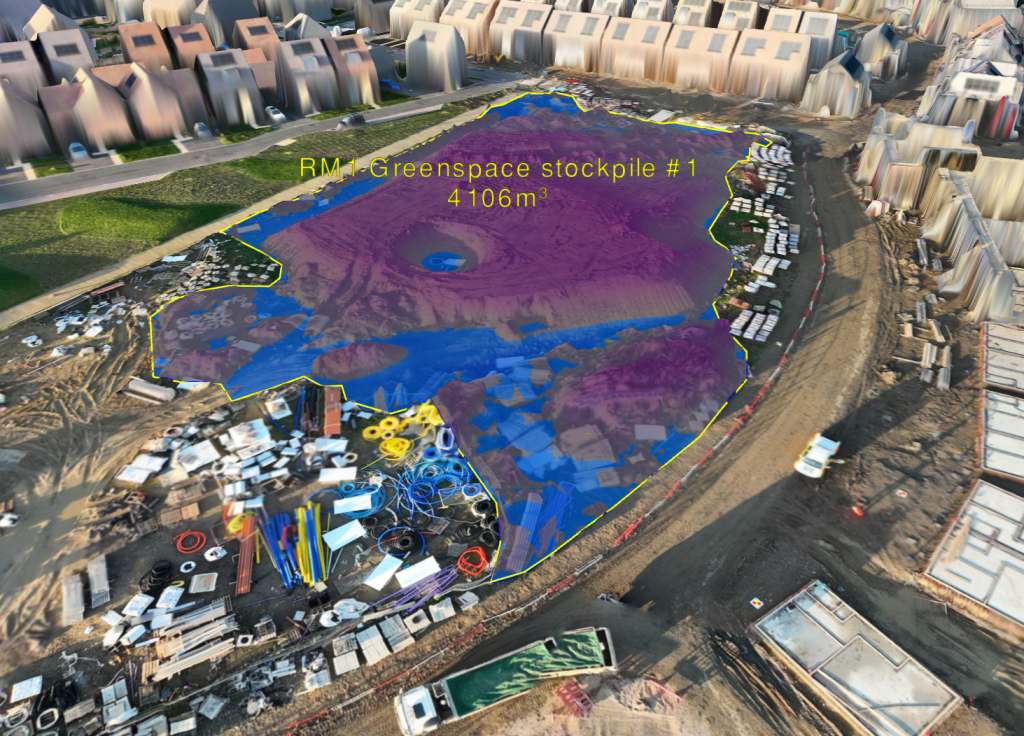
How do we use photogrammetry to assist our clients?
The most noticeable factors are time and money saved. A UAS can cover several square kilometres in a day, and if conditions allow for permanent ground control points we can even get the data to the client in the same day. This saves the client costs for our time on site, plus it opens up the opportunity for long range proactive decision making which saves more time and money further along the project timeline.
Less immediate but more important is the improvement to safety in the workplace. In a previous blog we touched on the serious impact of working at height can have on site safety.
50 people died in the construction sector as a result of falling from height in 2023/24. By introducing unmanned aerial systems into your routine operations we eliminate the need for working at height during condition and maintenance surveys which immediately improves your site safety, and reduces time spent on risk assessments and method statements. Further, by removing the requirement for expensive scaffolding and repeat survey visits, we reduce costs and timescales in the preliminary stages; and by building a model for the client to view at this stage we can reduce costs and time during the delivery phase of the work by identifying key areas for repair early on in the process.
Contact us for further information as to how our photogrammetry services can help you manage and maintain your built assets.