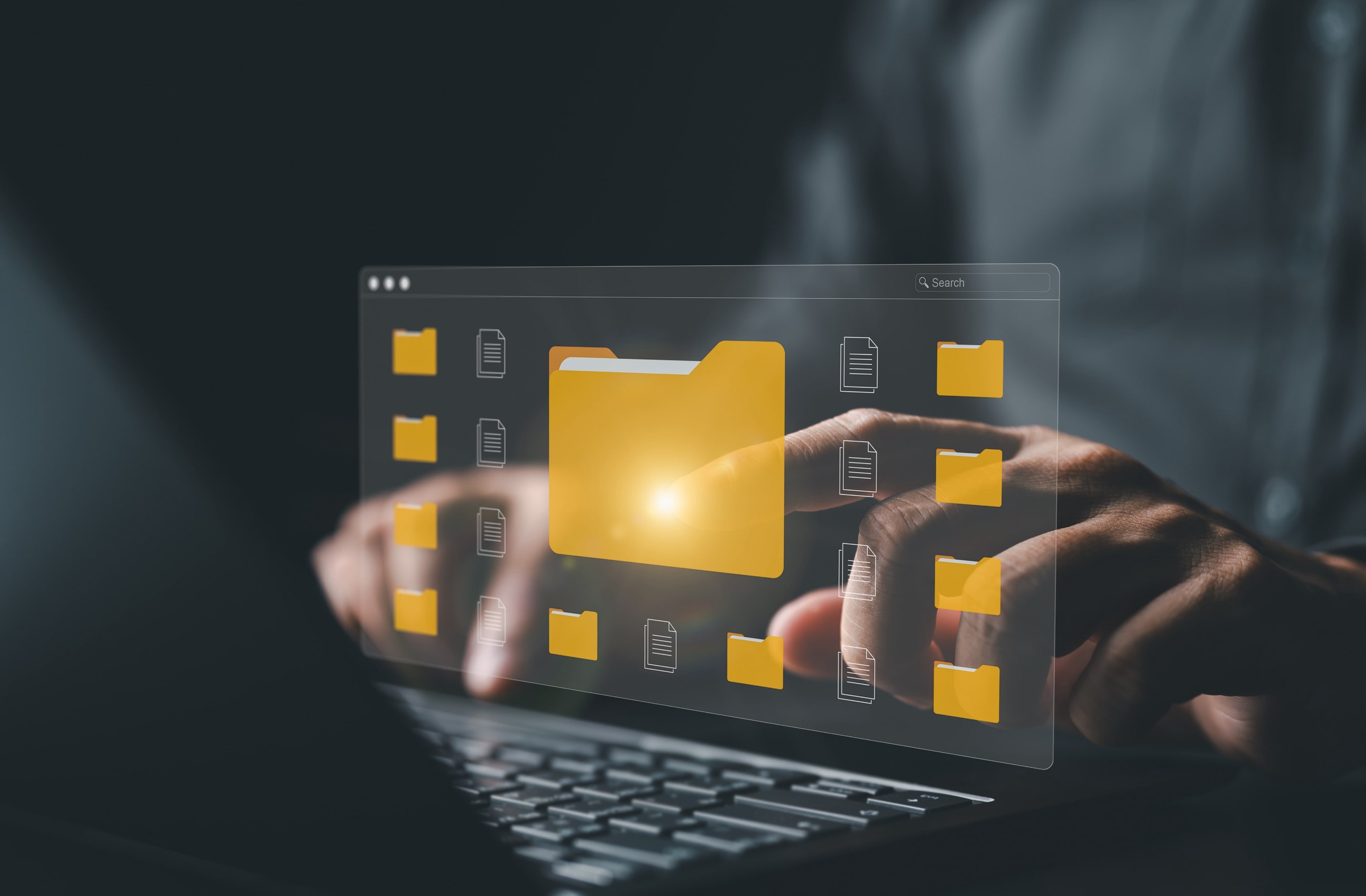
News
Once
Doing something once is a target we all strive for – unless it’s something we enjoy then it might get a second outing.
How much does a mistake cost in your part of this industry?
An approximation for comparison is £20,000 a night on a moderate sized highway scheme, and that only includes the cost of the bodies on site, we haven’t even started totalling up the cost of fuel, materials, plant, and machinery hire – then you have the CO² costs of getting everyone to site.
Some mistakes are unavoidable, but it is the ones that are avoidable we need to capture.
How do we manage mistakes? In the initial stages we do it through proper planning, surveys, and consultations with other stakeholders so we gain access to as much information as we can to build a better job. As we move into the mobilisation phase of the project, we undertake site visits and work with the designers so they can compare the historical data they have with what is on the ground. Then once everyone moves into the delivery phase we take the design drawings, the construction methods, the risk assessments, and all the other paperwork we have produced, and we as an industry go to work.
On time. On budget. Almost.
Absolutely everyone will tell you the preliminary phase lasts half as long as they would like and a large portion of that is taken up with rebuilding the tender award to include work that didn’t make the final cut but “now we’re here we might as well…”, all while ensuring the stakeholders have been consulted and the welfare has been arranged.
The mobilisation stage arrives while you’re still trying to sort out the issues left over from the preliminary phase, only to find out the designer and may not have had the latest data to design the scheme in because there aren’t any proper records. The Statutory Undertakers are contacted and send as much information as they have but will readily admit to not knowing what may or may not be present underground. So now we have to ask “trial holes or GPR?” and open a new line of enquiry.
The delivery phase comes up faster than any of us would like but the construction phase plan has been agreed, the F10 is signed off, the compound is set up, risk assessments and method statements are in place. The design is complete – but we all understand no plan survives contact with a shovel, so with some collaborative interpretation we can figure out what can go where, and a few follow up calls will resolve most of the sticking points.
Then the trial holes get dug and the design needs to change. Work stops, we make the site safe, and we all go back to the meeting room. But the costs don’t stop. Operatives need paying, plant and machinery have hire costs, material suppliers need paying for what they have supplied, any prefabricated items that need to change will have additional costs assigned to them. The sound of Early Warnings and Compensation Events marching inexorably toward the project manager’s desk can be heard…
Sound familiar? If only everything could be Option E…
We have found the key for our clients in the Tier 1 and Tier 2 game is to jump into the planning and wrestle with it. Which isn’t always possible with the resources on hand; and while you can pull people into meetings and give them actions, if you are stretched to the point you can’t follow up then things will slip. This is where VM Group comes in we have been jumping in and wrestling the details in the preliminary and planning stages so their delivery teams only have to do the job once.
Because in this industry every time we do something more than once, we increase the risk of harm or danger, we cost the environment, and we also cost people money.